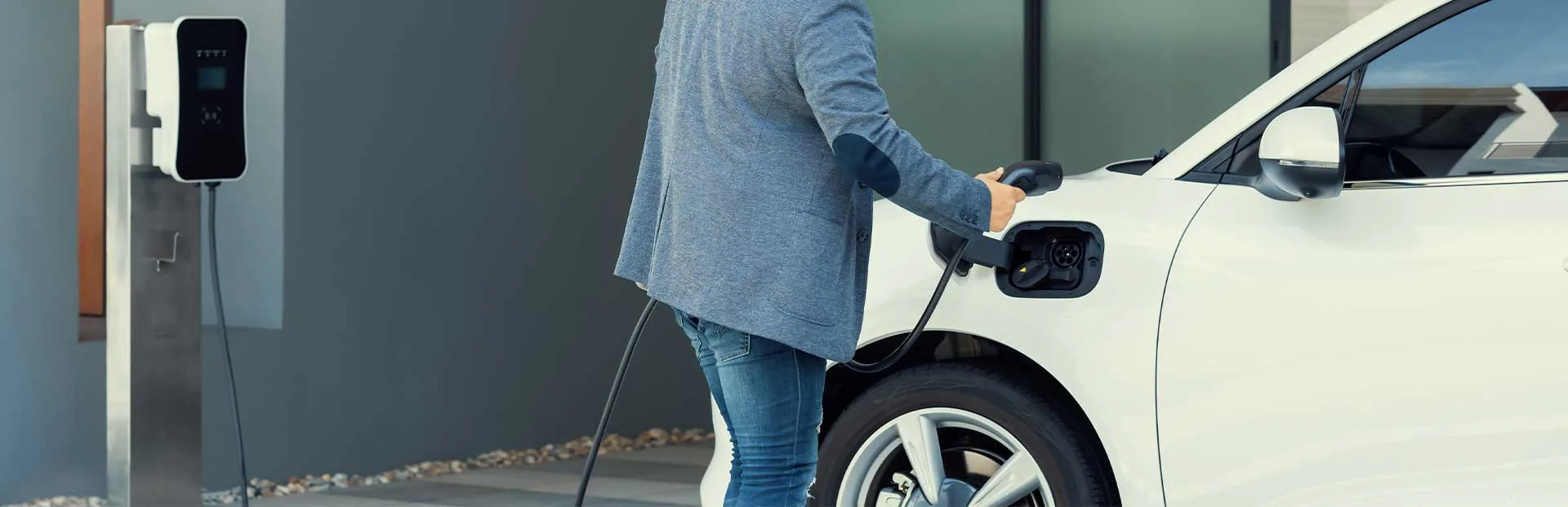
CASE 3
SPvolt Two-Year Quality Assurance Service Empowers European Start-up Charging Equipment Company Case
Customer Background
A European start-up charging equipment sales company focuses on the sales of electric vehicle charging cables and adapters. In the industry, the quality assurance period for similar products is mostly one year. As a brand new to the market, this company urgently needs to enhance its competitiveness through more reliable after-sales guarantees, win consumers’ trust, and expand in the European market.
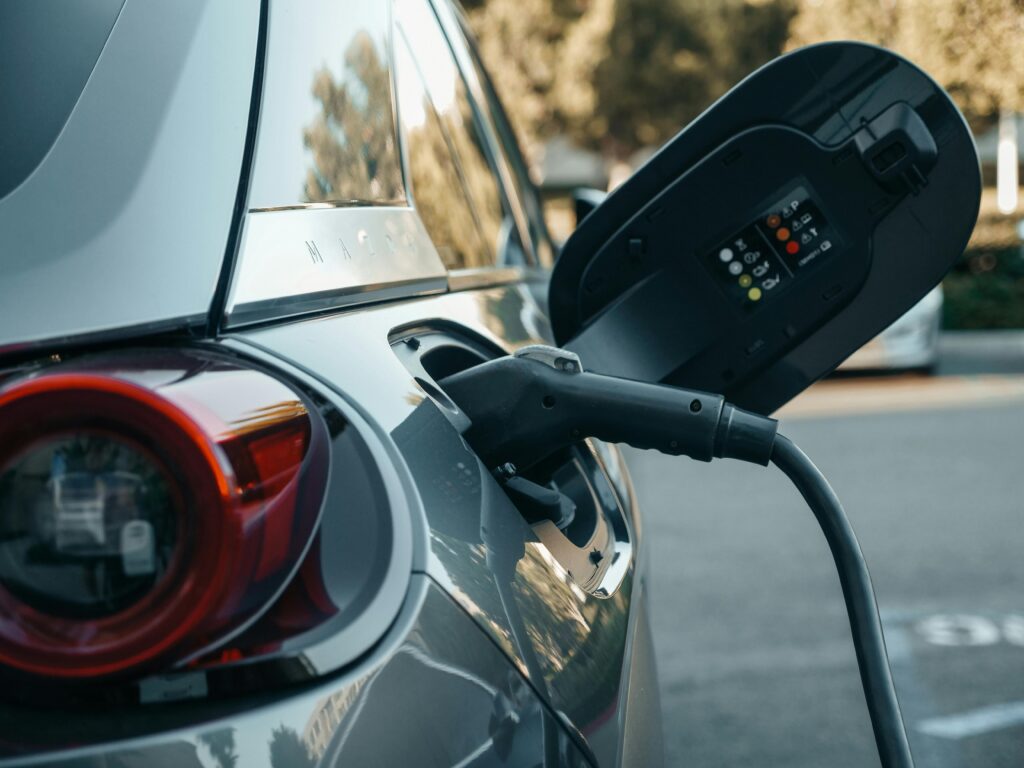
Solutions
Strict Selection of High-Quality Materials to Lay the Foundation for Quality Assurance
Cable Materials: The outer sheath of the charging cable adopts TPU (Thermoplastic Polyurethane Elastomer), which has excellent wear resistance, weather resistance, and low-temperature flexibility, adapting to the diverse climatic environments in Europe. The internal conductor uses high-purity copper, with high conductivity and low resistance, reducing usage loss and failure probability.
Adapter Components: The core conductive terminals adopt a three-layer electroplating process (first plating 2μm red copper, then plating 3μm nickel, and finally plating 3-5μm silver). The oxidation resistance and wear resistance far exceed the single-layer silver plating process of peers, ensuring product durability from the source.
Full-process Quality Control to Ensure Reliability
Production Inspection: During the production of each batch of cables, 10 indicators such as the thickness of the insulation layer and the firmness of the conductor connection are sampled and inspected. Before the adapter leaves the factory, it undergoes 10,000 plug-in and pull-out tests to ensure connection stability.
Simulation Test: Aiming at the complex environment in Europe, simulate tests such as high and low-temperature cycles from -30℃ to 50℃ and humidity changes are carried out to ensure stable product performance in different scenarios, providing quality support for the two-year quality assurance.
Perfect After-sales System to Fulfill the Quality Assurance Commitment
Establish a 24-hour rapid response mechanism. For products with non-human damage during the quality assurance period, new products will be replaced free of charge. Reduce the after-sales cost of customers and the usage concerns of consumers.
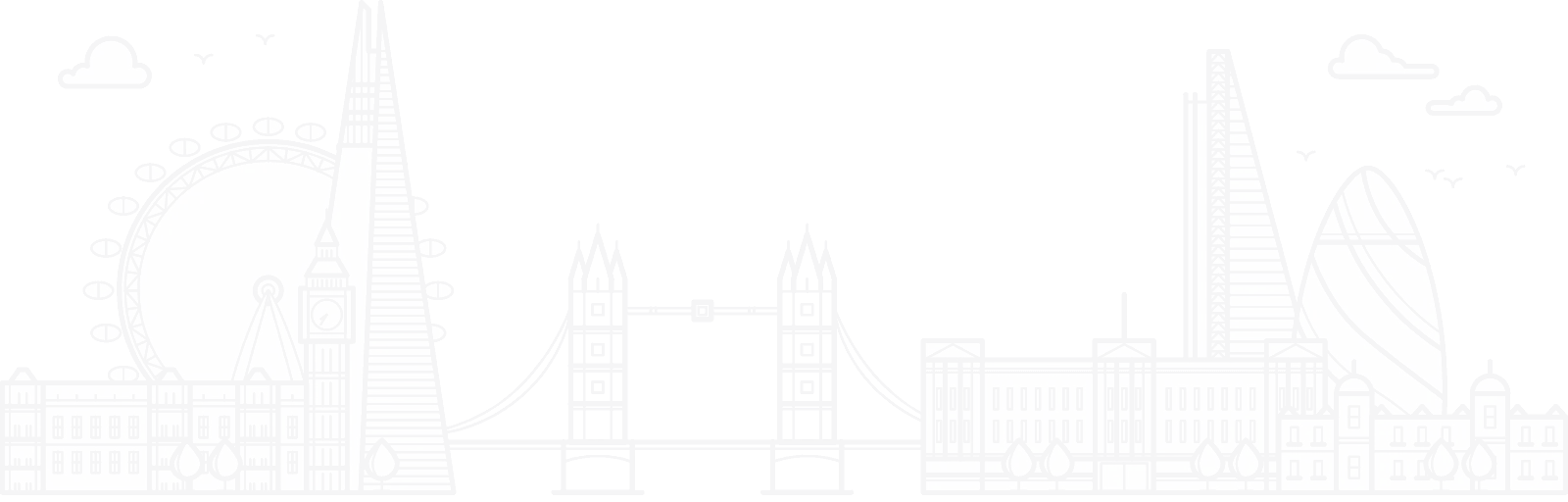
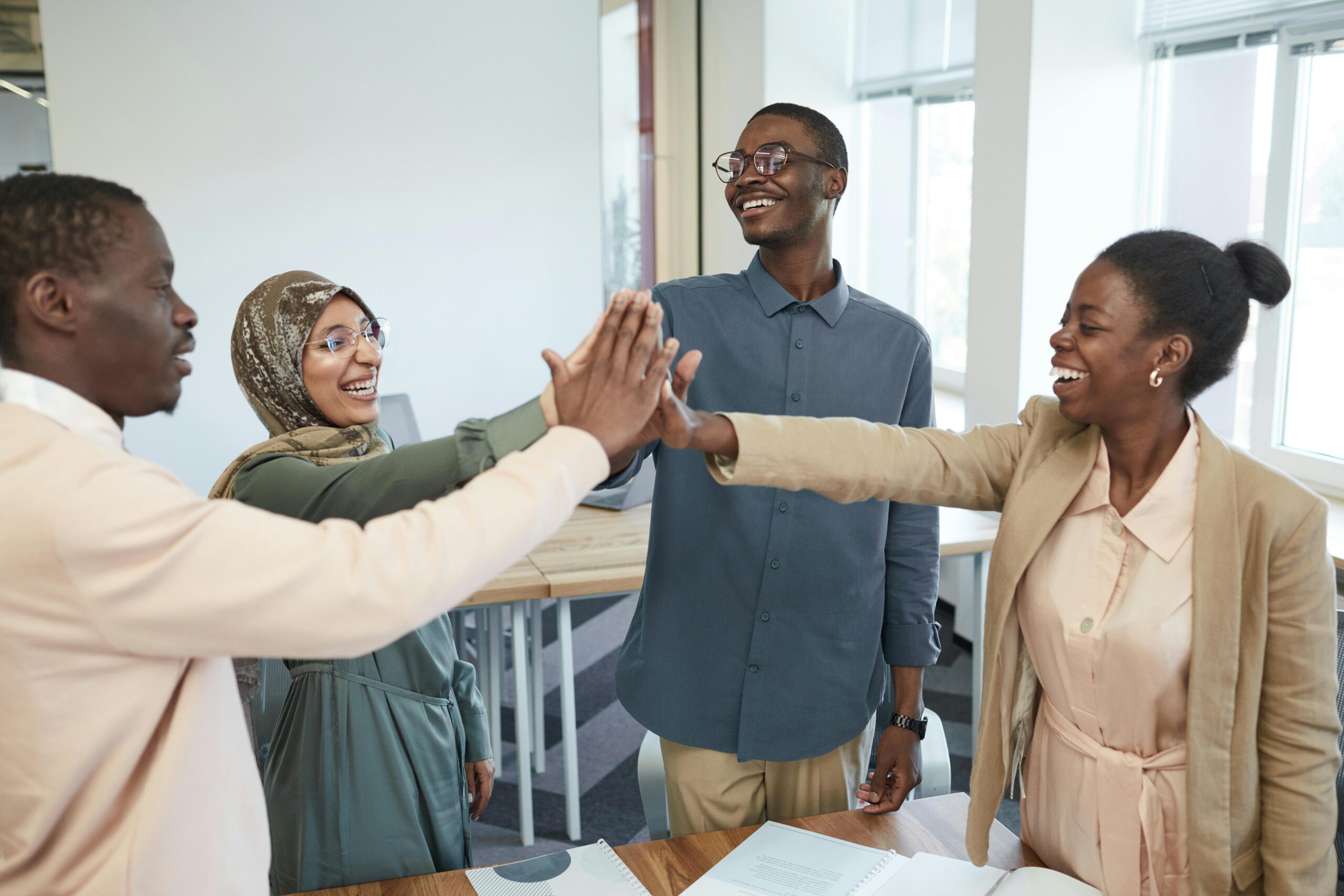
Cooperation Achievements
- Enhanced Consumer Trust: The two-year quality assurance has enhanced the product’s recognition in the European market, increasing the purchase rate of new customers by 30% within six months.
- Optimized After-sales Cost: Strict quality control has reduced the product failure rate to only 3% (about 8% in the industry), and the actual after-sales replacement cost is controllable.
- Expanded Market Share: Relying on reliable quality assurance, the company has cooperated with many small and medium-sized charging stations in Europe. The sales volume has increased by 50% within one year, successfully gaining a foothold in the European charging equipment market and verifying the promoting effect of the two-year quality assurance on the business.
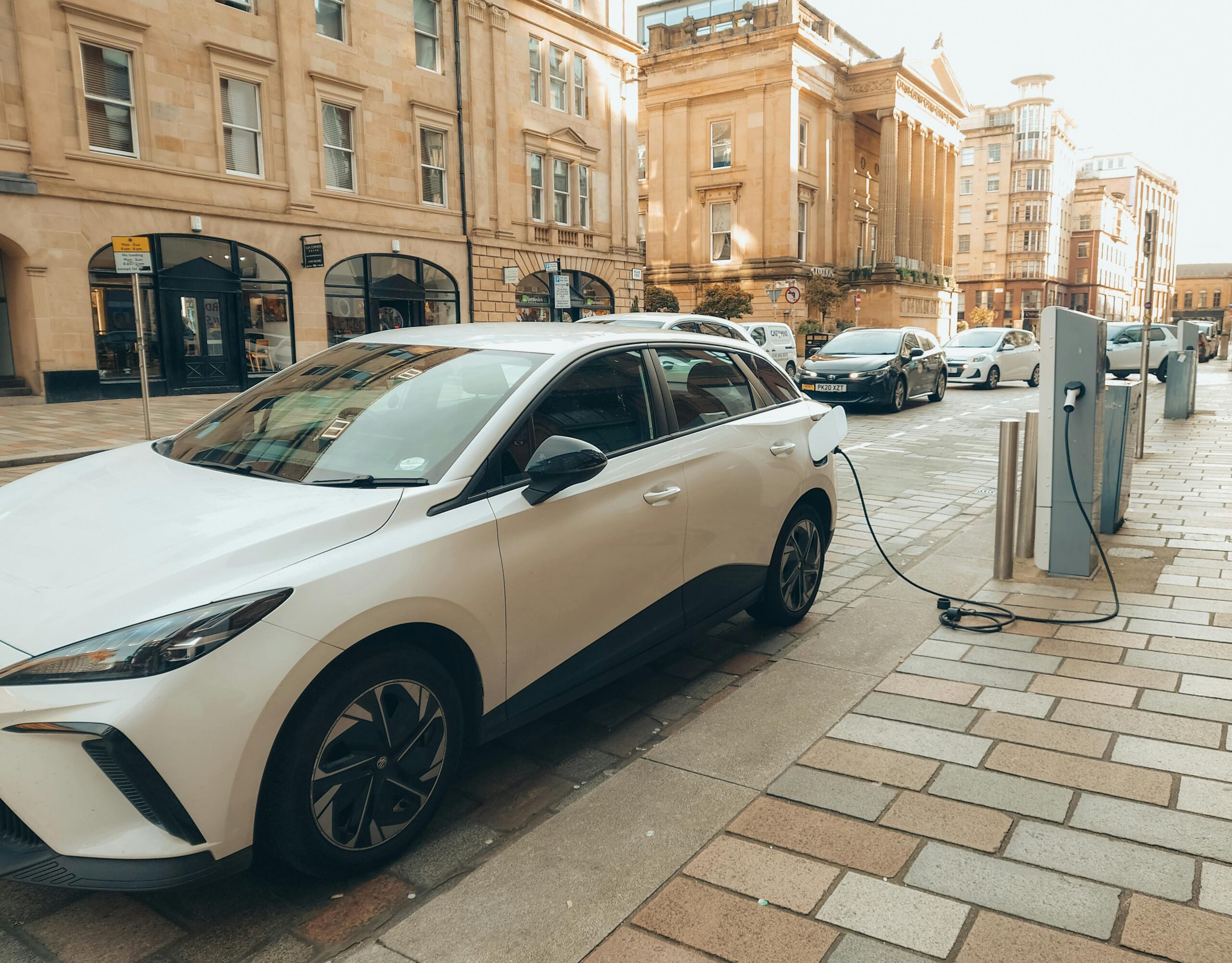
Case 1
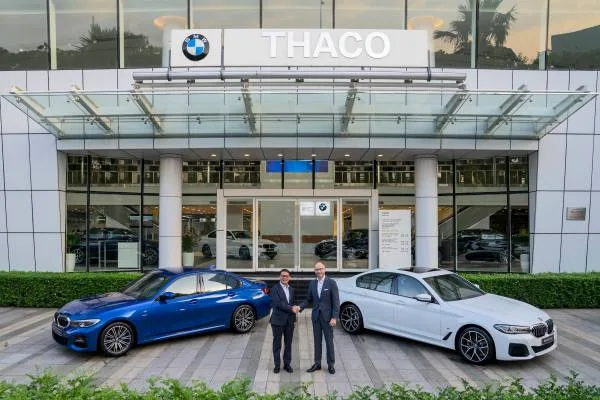
Case 2
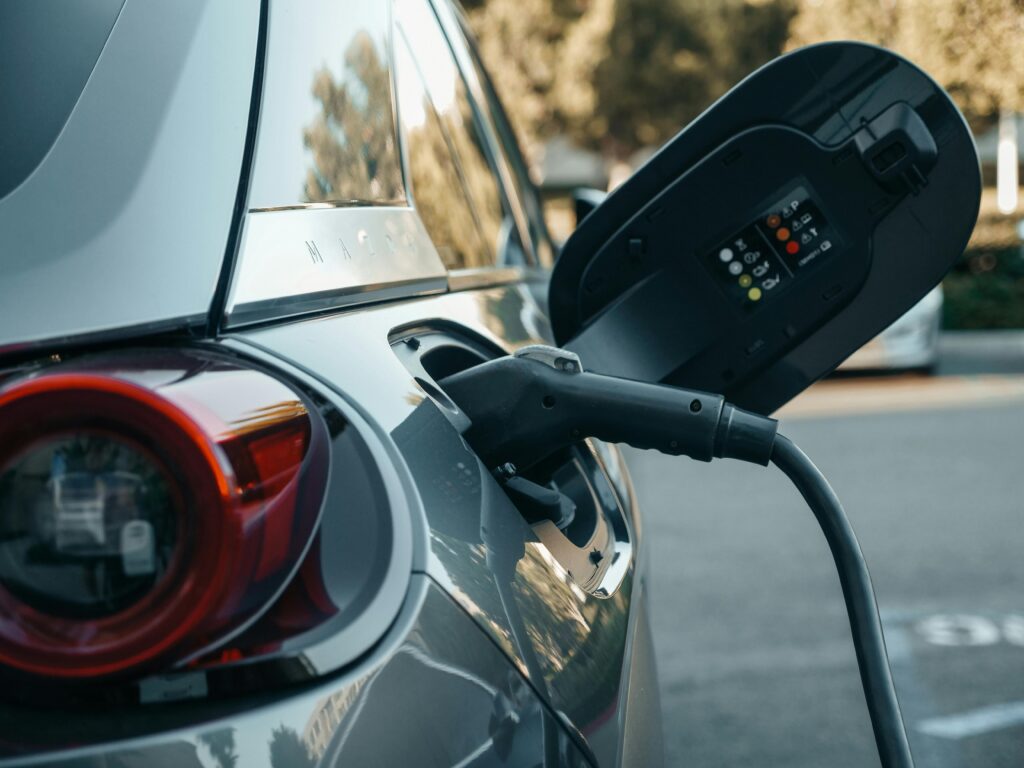
Case 3
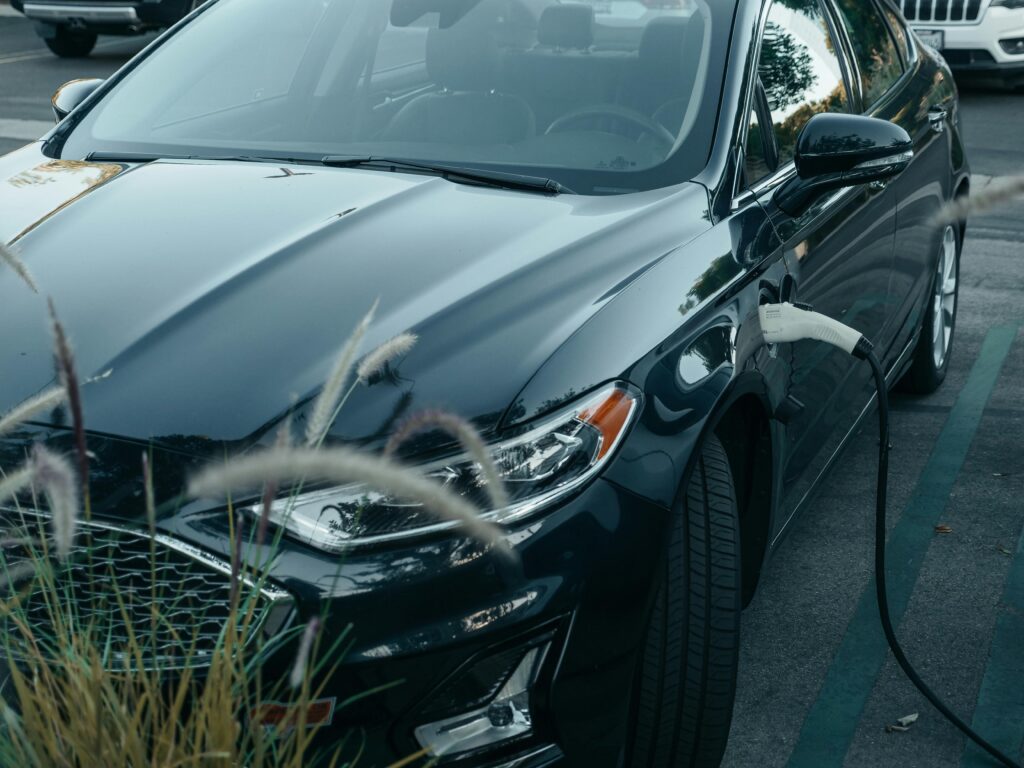
Case 4
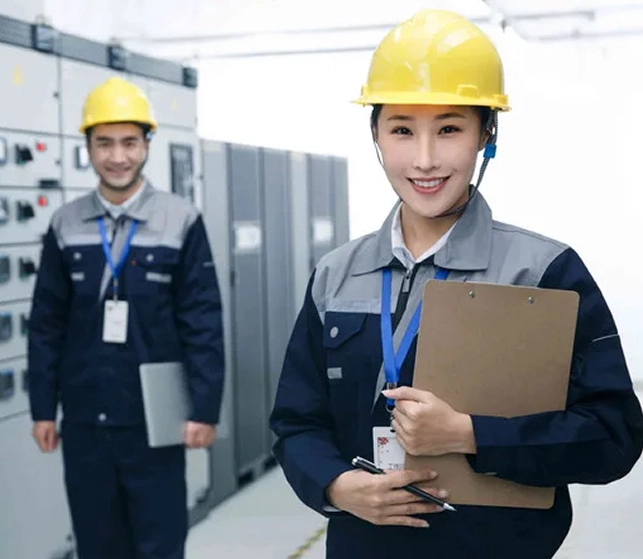
Ready to start your EV Charging Brand?
Contact us for custom solutions and technical support!